Client Background
A leading pharmaceutical manufacturer specializing in sterile injectable drugs faced critical challenges in maintaining stringent environmental controls within its ISO Class 5 cleanrooms. The company required ultra-precise differential pressure monitoring between production zones, buffer areas, and adjacent corridors to prevent cross-contamination and ensure compliance with Good Manufacturing Practice (GMP) regulations. Existing differential pressure sensors struggled with drift, frequent manual recalibration, and unreliable performance in hazardous areas, risking production downtime and product quality.
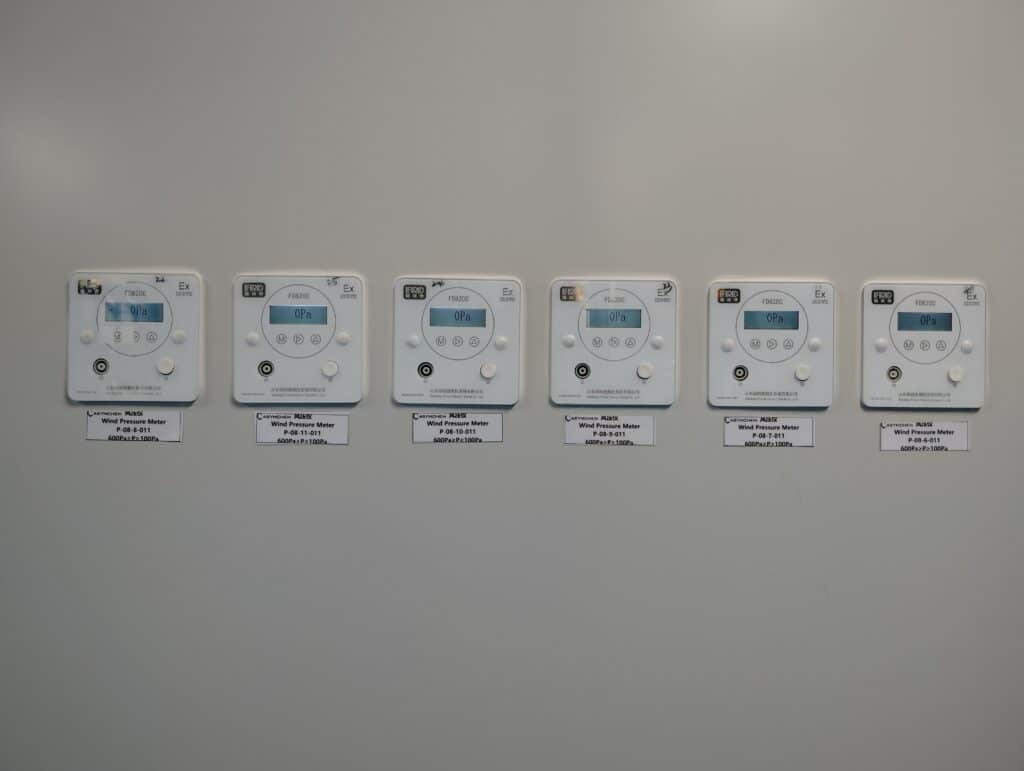
Challenges
1、Precision & Stability: Minor pressure fluctuations (as low as 10–50 Pa) between cleanroom zones demanded measurement accuracy ≤±0.5% to prevent airflow reversals.
2、Maintenance Burden: Traditional transmitters required weekly manual zero-point adjustments, increasing labor costs and operational disruptions.
3、Safety Compliance: Sensors needed intrinsic safety (Ex ia IIC T4 certification) for use in hazardous environments where alcohol-based disinfectants were present.
4、Integration Complexity: Legacy devices lacked digital communication capabilities, hindering real-time data integration with the facility’s Building Management System (BMS).
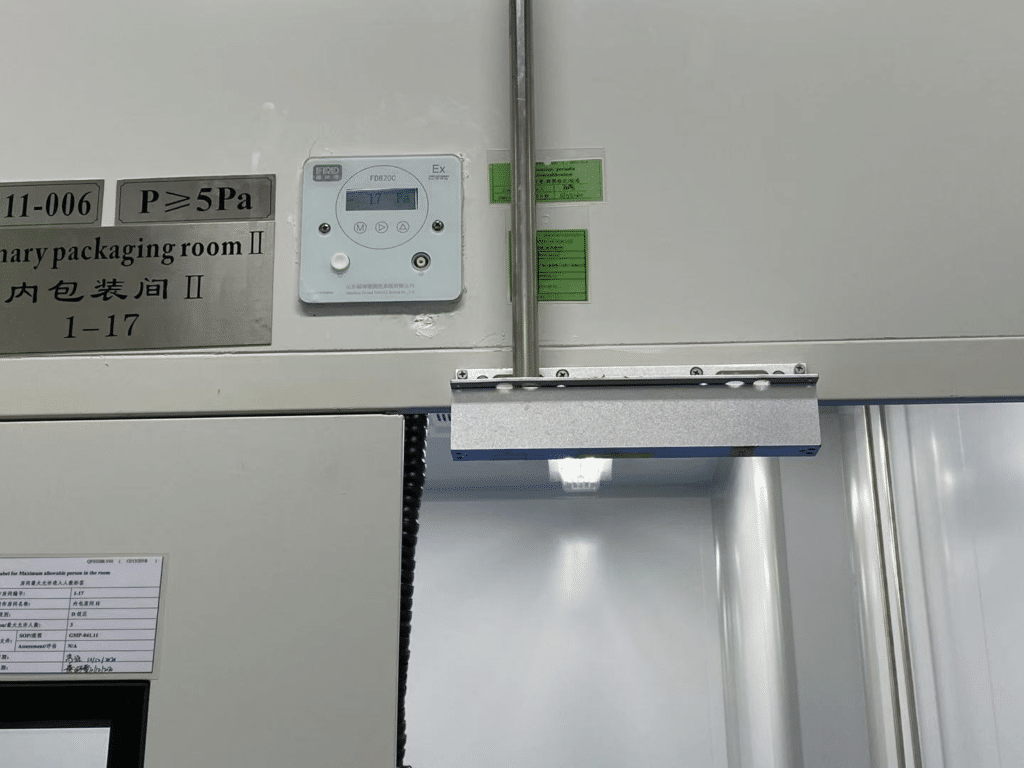
Solution: FD820C Embedded Micro Differential Pressure Transmitter
FRD CONTROL FD820C was selected for its innovative features tailored to pharmaceutical cleanroom requirements:
1、High Accuracy & Flexibility
Configured with 0.5% full-scale accuracy and a 0–500 Pa range to detect minute pressure changes between critical zones.
Dual-range capability allowed monitoring of both ultra-low differential pressures (e.g., airlocks) and higher pressures (HEPA filter status).
2、Real-Time Automatic Zero-Point Calibration
The patented online auto-zeroing feature eliminated drift caused by temperature shifts or mechanical vibrations, ensuring continuous accuracy without manual intervention. This reduced calibration workload by 80% compared to previous systems.
3、Explosion-Proof Design
Intrinsically safe construction (Ex ia IIC T4) enabled safe operation in hazardous areas where flammable vapors might exist.
4、Seamless Integration
It has analog output of 4-20mA, or RS485 + relay output, and adopts the MODBUS RTU protocol, which can transmit real-time data to the Building Management System (BMS). It is capable of automatically issuing alarms for pressure deviations. After being integrated with the Supervisory Control and Data Acquisition (SCADA) system, it enables remote monitoring of multiple cleanroom areas.
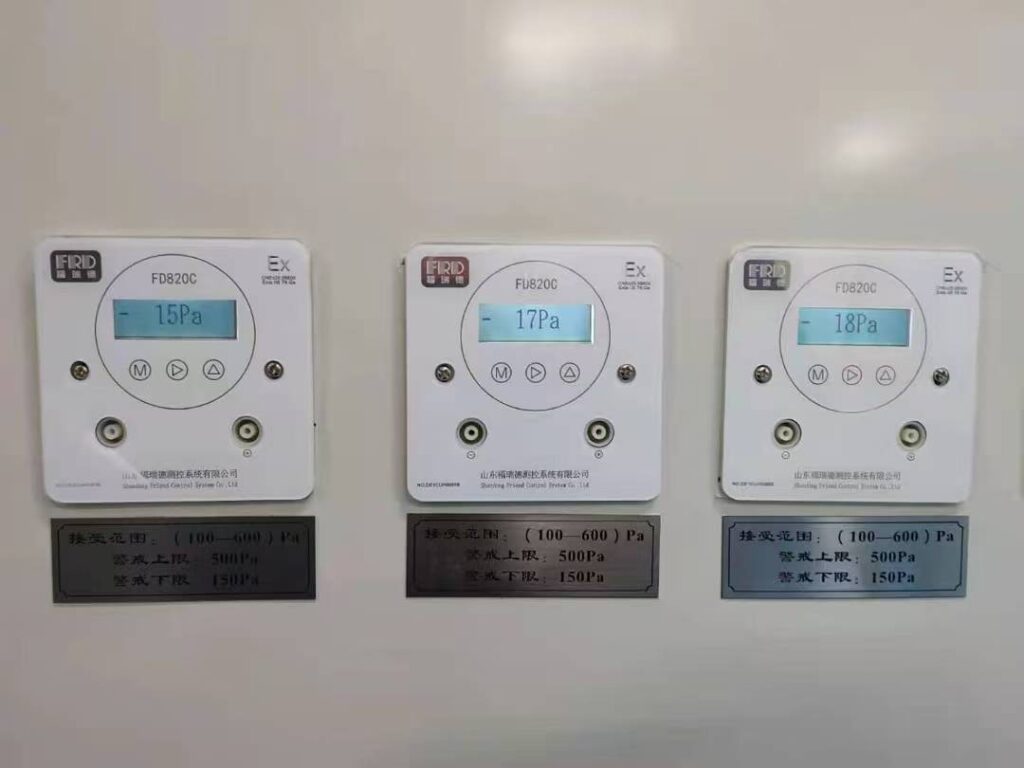
Implementation
1、Deployment Areas: FD820C units were installed at critical junctures, including:Between lyophilization suites and adjacent washrooms to maintain negative pressure.At HVAC supply/exhaust ducts to monitor HEPA filter integrity.In gowning rooms to ensure positive pressure gradients.
2、Calibration: Factory-preconfigured auto-zeroing intervals (self-configurable) were customized to align with cleanroom sanitization cycles.
Results
1、Enhanced Compliance & Product Quality
Pressure stability improved by 60%, maintaining gradients within ±2 Pa of setpoints. Zero GMP non-conformities related to environmental controls were reported post-installation.
2、Reduced Operational Costs
Maintenance labor decreased from 15 hours/week to 3 hours/month, saving approximately $18,000 annually.
Elimination of unplanned downtime due to sensor drift reduced production losses by an estimated $250,000/year.
3、Safety & Scalability
Hazardous area compliance simplified audits, while MODBUS connectivity supported future IoT-enabled upgrades.
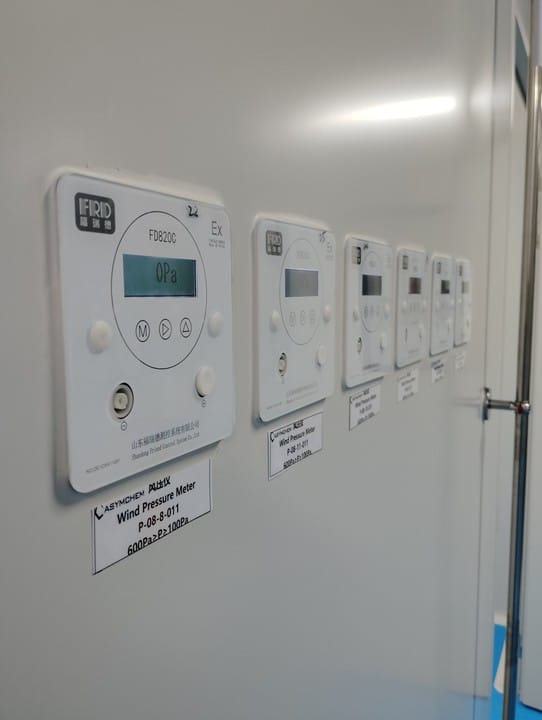
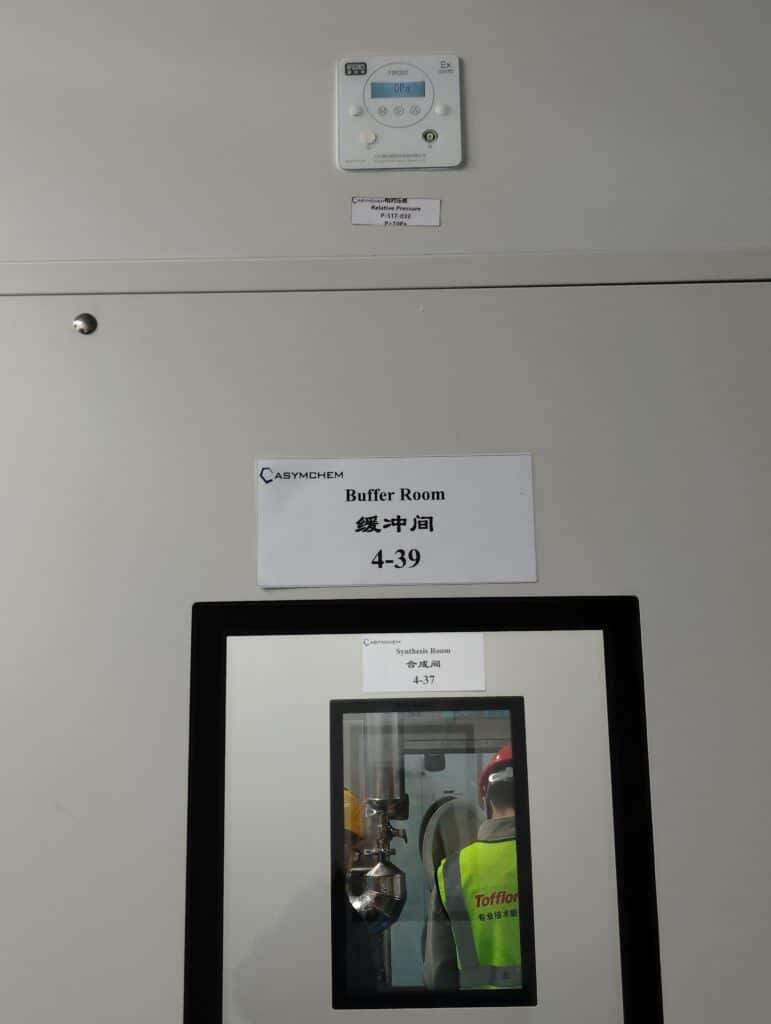
Client Feedback
“The FD820C’s auto-zeroing feature has been a game-changer. We’ve achieved unprecedented control over cleanroom pressures, which is vital for sterility assurance. Its reliability in explosive atmospheres and seamless BMS integration make it indispensable to our operations.”
— Chief Engineer, Facility Management
Conclusion
FRD CONTROL FD820C exemplifies how innovation in precision instrumentation can address critical challenges in pharmaceutical manufacturing. By combining patented technology, robust safety design, and smart connectivity, it has become a cornerstone of modern cleanroom pressure management, driving efficiency, compliance, and cost savings in highly regulated environments.