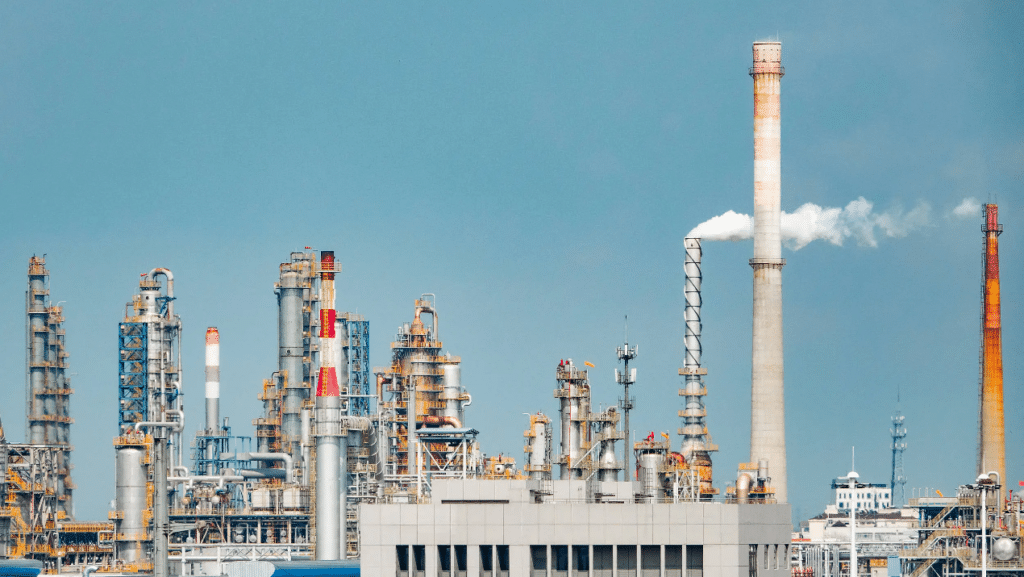
I. Customer Background and Challenges
A chemical enterprise’s chemical storage tanks are responsible for transporting slightly corrosive, flammable, and explosive materials such as alcohols and alkanes to reaction kettles through pipelines. The production process has extremely high requirements for the accuracy, stability, and safety of pressure monitoring.
The traditional pressure transmitters previously used had obvious shortcomings: insufficient measurement accuracy, serious data drift during temperature fluctuations or changes in medium characteristics, making it difficult for the control room to accurately judge the pipeline pressure status; fixed range with a narrow coverage, requiring frequent shutdowns to replace equipment when facing pressure differences in different material transportation, affecting production continuity; low equipment protection rating, frequent failures in the humid, dusty, and strongly electromagnetically interfered environment of the machine room, and non-explosion-proof design that cannot meet the safety specifications for flammable and explosive scenarios, posing significant safety hazards; in addition, the analog signal transmission method caused lag in data interaction between the site and the control room, with a large workload for manual calibration and patrol, resulting in low operation and maintenance efficiency.
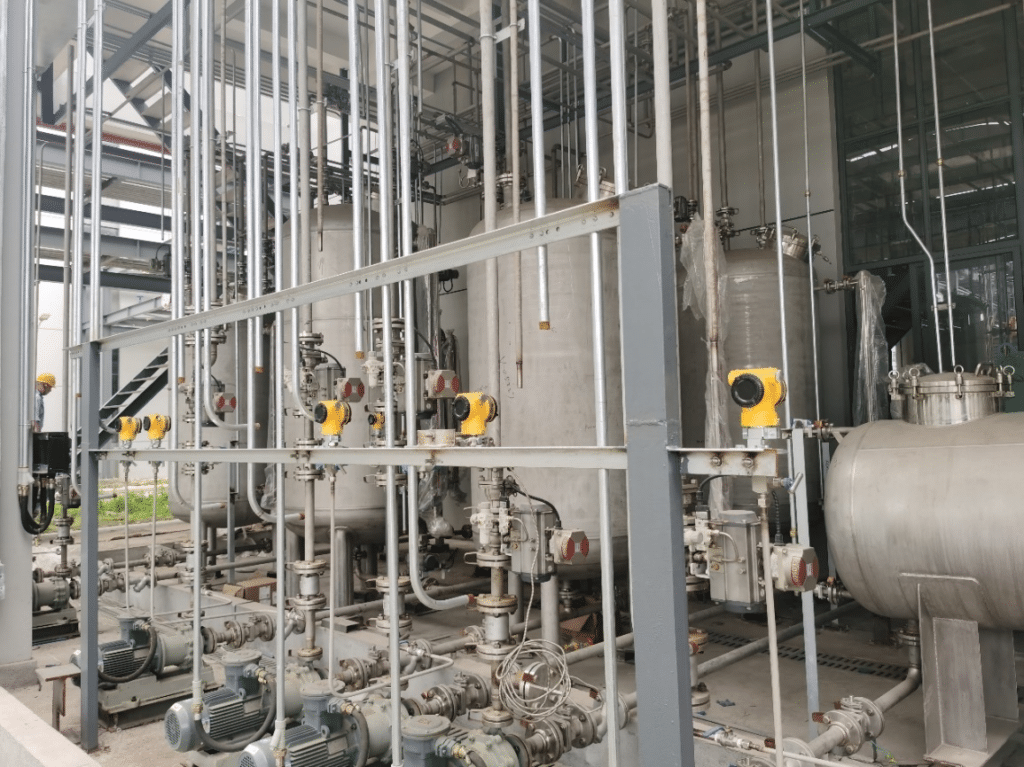
II. Solution Implementation
To overcome the above bottlenecks, Friend Control carried out a systematic upgrade of the transmitter for the complex working conditions of the company’s machine room:
1. High Precision and Environmental Adaptability
Using internationally advanced single-crystal silicon core, combined with precise digital temperature compensation and nonlinear correction technology, it can maintain stable pressure signal output even in the working conditions of frequent pressure changes in slightly corrosive pipelines such as alcohols and alkanes, with a maximum accuracy of ±0.075%F.S, avoiding control misjudgment caused by measurement deviations. It completely solves the problem of frequent equipment replacement due to insufficient measurement range and can remotely adjust the measurement range parameters through the HART375 handheld communicator without shutdown.
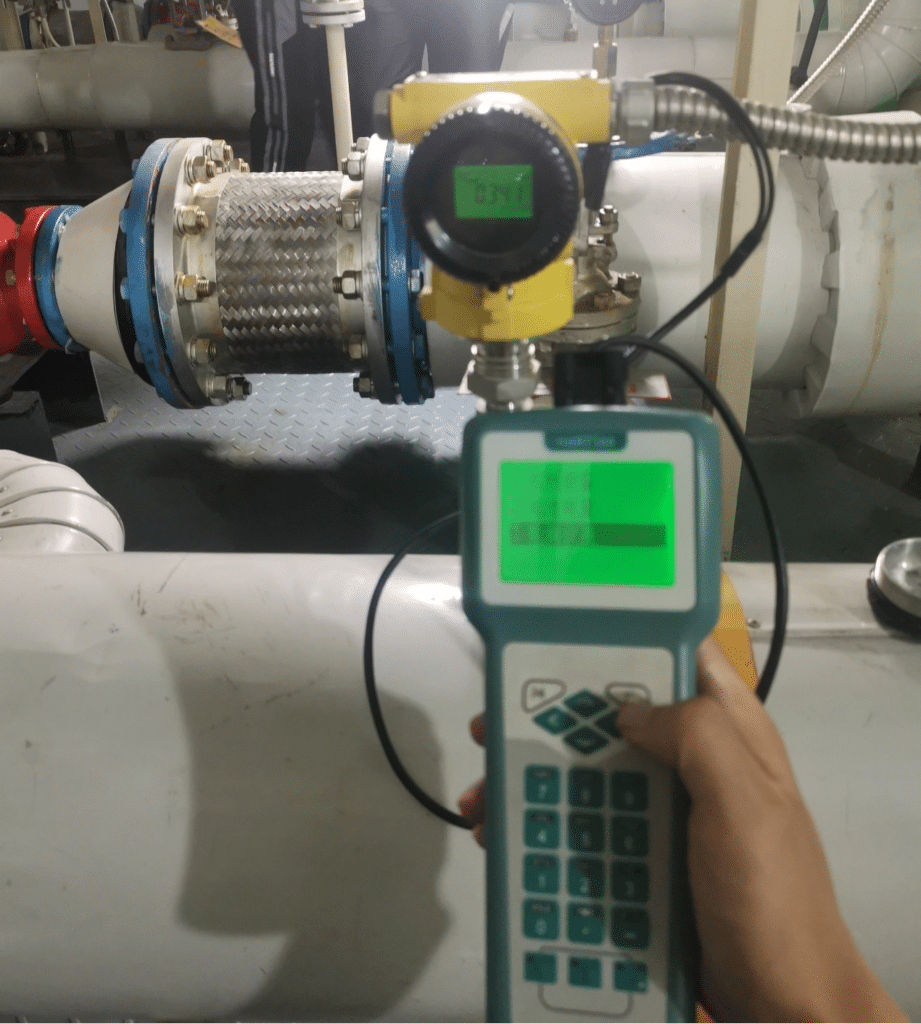
2. Safety Protection and Reliable Communication
For flammable and explosive environments, the explosion-proof structural design of the transmitter complies with the GB3836 standard and can be directly installed in dangerous areas such as methanol 输送 (transportation) pipelines without additional safety modifications, eliminating the risk of explosions caused by electric sparks from the hardware level. At the same time, the IP65 protection rating effectively resists the dust in the machine room and extends the service life of the equipment.
In terms of signal transmission, the digital circuit design supporting the HART protocol realizes seamless docking with the control room’s DCS system. Technicians can also remotely read multiple parameters and perform equipment diagnosis in the control room, greatly reducing the frequency of manual patrols and calibration work.
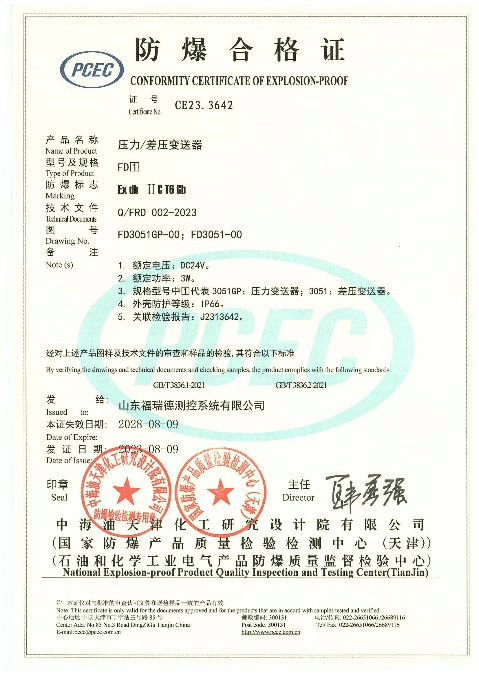
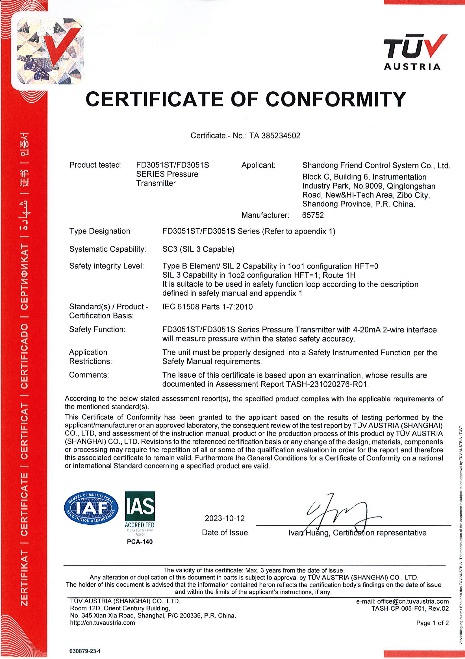
3. Operational Convenience and System Compatibility
The on-site button zeroing function of the transmitter simplifies the daily calibration process, and operators can quickly complete zero adjustment without complex tools; the standardized signal output and protocol compatibility enable it to easily integrate into the enterprise’s existing automation control system, achieve linkage control with equipment such as pipeline valves and flowmeters, and build a more intelligent material transportation monitoring system.
Based on the above characteristics, Shandong Friend Control System Co., Ltd. recommends the use of the FD3051ST pressure transmitter for it.
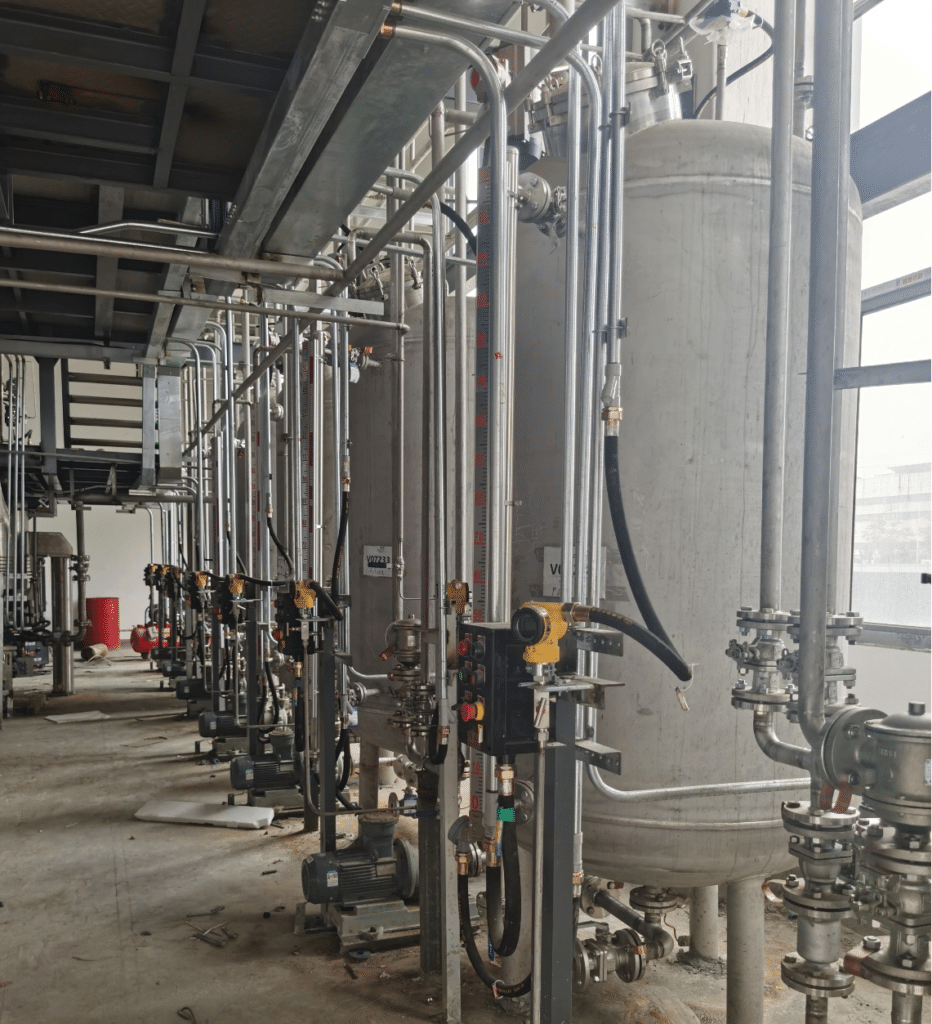
III. Application Results
After the FD3051ST pressure transmitter was put into use, the pressure monitoring effect of the chemical storage tanks was significantly improved: the stability and reliability of pressure data were greatly enhanced, the control room could real-time and accurately grasp the pipeline pressure status, and the problems of control lag and misjudgment in the material transportation process were fundamentally solved; the wide measurement range design and remote operation function completely got rid of the trouble of frequent shutdowns for equipment replacement, and the continuity of the production process was effectively guaranteed; the explosion-proof and protection performance allowed the equipment to operate stably in high-risk environments, eliminating safety hazards; the digital interaction and convenient maintenance design reduced the frequency of manual intervention, making operation and maintenance more efficient and convenient.
Conclusion
Through the application of the FD3051ST pressure transmitter, the enterprise successfully achieved the intelligent upgrade of pressure monitoring for chemical storage tanks, providing a solid guarantee for the safe, stable, and efficient operation of the material transportation link, and becoming a typical reference solution for similar chemical enterprises in the field of pressure measurement.